New materials for next-gen auto parts
- Robyn Quinn
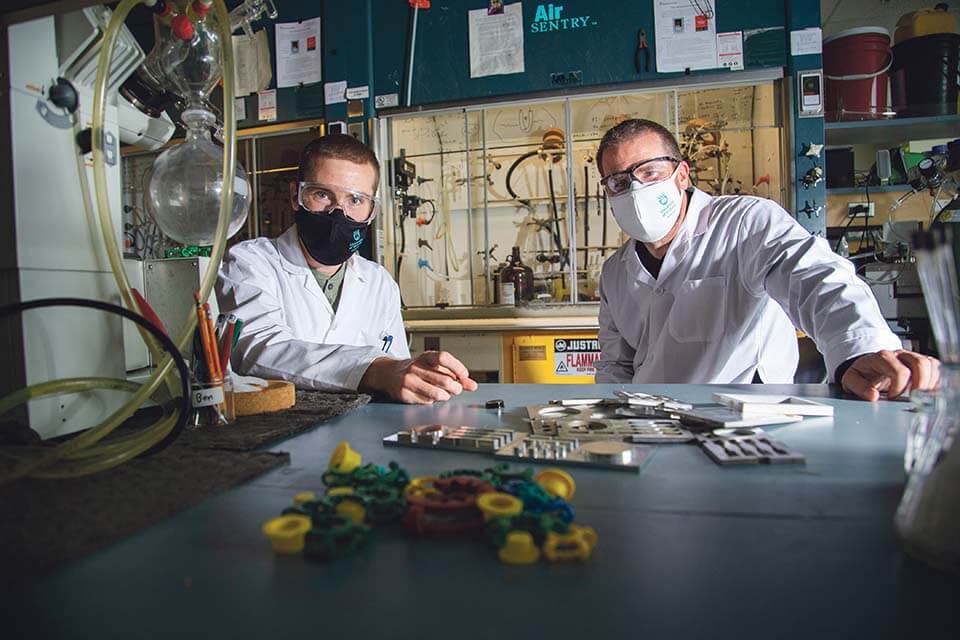
In dim light, a line of armoured vehicles slowly snakes through narrow streets. The driver in the lead vehicle focuses on the road ahead but is cautious of possible threats. Suddenly, an explosion in the road rocks the caravan. Several vehicles receive damage but all arrive safe at their destination. The passengers and drivers are all unharmed but the damage to the largely metal vehicles is severe enough to write them off.
The cost of secure transport, whether with military or law enforcement, can be steep. Up until now there were limited options available to protect the vehicles and passengers inside.
Thanks to the work being done by University of Victoria chemistry graduate student Ben Godwin and his faculty supervisor Jeremy Wulff, there are now new materials on the horizon that are lighter and stronger than ever before. Even better, these advanced new materials are able to better dissipate energy and, potentially, be repaired in the field.
Recently, Godwin shared how one small change to the structure of a common thermoset plastic called “polydicyclopentadiene”—the addition of a single atom—produced a versatile new polymer. The new material is stronger and stiffer than the parent plastic, and could have the strength to withstand significant impact from bullets or explosives, while remaining durable under extreme temperatures. “A lot of people are excited about this change and what we can do now with the newest version,” explains Godwin, “many more commercial applications are possible.”
According to Wulff the polymer can make a big difference for existing manufacturing, “Even adding just five per cent allows for amazing enhancements like incorporating drug compounds that can fight bacteria, attaching special paints or building in florescent properties to glow in the dark.”
Using this polymer could also increase the fuel economy of consumer vehicles.
The easiest way to improve the fuel economy of a vehicle is simply to have less weight. By replacing metal parts with durable plastic parts a significant weight reduction can be achieved at low cost.
—Ben Godwin, UVic chemistry graduate student
Godwin was also able to eliminate the unpleasant odour of the polymer’s predecessor. Because of that, the new polymer can be used on the interior as well as the exterior of the vehicle.
The polymer project at UVic is now in its sixth year and has already spun off one student-founded enterprise called Poly V. Technology Inc., launched by PhD researcher Tong Li. The growing list of potential commercial uses and sectors include forestry, law enforcement, natural resource management.
EdgeWise
What’s the difference between polymers and plastics? All plastics are polymers, but not all polymers are plastics. The word “polymer” refers to any large molecule made up of repeating units. The DNA in our cells is a polymer, as is the protein in our food. When the repeating units that the polymer is made from—called “monomers”—are things like ethylene or stryene that come from petroleum feedstocks, then the resulting polymer is called a plastic.
Plastics are ubiquitous in our society, but plastic waste is an enormous problem. Understanding the chemistry of polymer materials is key to designing materials that don’t persist in the environment.
Commercial plastics can be divided into two broad categories. Thermoform plastics (thermoplastics) are linear chains of repeating monomer units. These melt at high temperatures and can be reformed into new objects. Unfortunately, this can lead to weaker materials with each round of re-processing.
Thermosetting plastics (thermosets) have extra bonds (called “crosslinks”) between the linear polymer chains. Thermosets don’t melt, making them useful in applications where high-temperature performance is required. Silicone used in kitchen bakeware is a thermoset polymer.
Since they can’t be melted and reformed, recycling of thermosets is difficult. However, researchers around the world—including the Wulff group at UVic—are inventing new kinds of tough, recyclable thermosets that can be reprocessed multiple times without affecting their mechanical properties.
Photos
In this story
Keywords: research, chemistry, graduate research, sustainability, technology, community, international, sustainability, administrative
People: Ben Godwin, Jeremy Wulff
Publication: knowlEDGE